Soy Doesn’t Stop: How Soybeans Come Back to the Farm
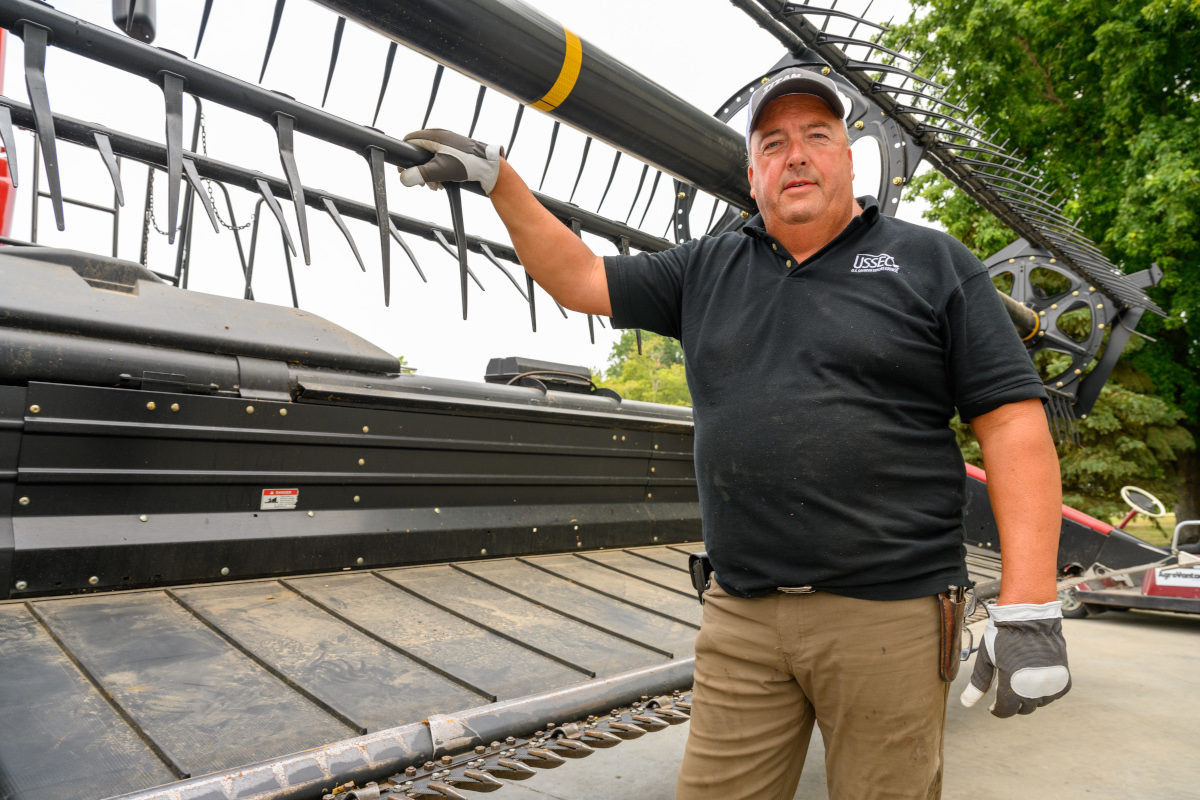
Take a walk around Jay Myers’ farm near Colfax, North Dakota, and it becomes evident that soybeans are more than just a crop to him. The bountiful soybean fields that surround his home are only the beginning of soy at his farm.
Myers and many other farmers see the beans they grow being used in more than a thousand different products.
To increase and diversify demand for U.S. soybeans, the checkoff supports innovative research that leads to the development and commercialization of new sustainable, high-performing products that use soy each year. In fact, in the last decade industrial use — besides the oil used for biodiesel — of soybean oil in the U.S. increased by more than 50 percent.
From soy-based asphalt to concrete durability enhancer to belts and tires on his combine, the oilseed Myers grows is intertwined with his farming operation through these and many other innovative products.
“There’s a lot of new uses for all of these soybeans,” Myer says, looking out at his late-summer fields. “We recently added a soy-based dust suppressant to the floor of our machine shed and will be using a soybean-based sealant to protect our concrete.”
For the fourth year, Myers is using RAPTOR® rubber draper belting with TerraTech™ technology on his combine, which was developed in partnership with the soy checkoff. The patented rubber technology uses soybean oil instead of petroleum in a rubber compound with many applications. Each of the belts produced by WCCO Belting in Wahpeton, North Dakota, is made with the oil from about .75 bushels of soybeans.
WCCO Belting is a 67-year-old, family-owned custom rubber product manufacturer serving the agriculture, light industrial, construction, sand and gravel, packaging and recycling industries worldwide. The company focuses on the technological advancement of each raw material and belt component to provide high-value rubber product solutions.
“The performance of the belts is at least the same as belts made with petroleum products,” says Jean Voorhees, Vice President of business development at WCCO. “We’ve also seen that during testing, the soy belt provided about 20 percent more abrasion resistance than a petroleum-based belt.”
The belts were developed with research support from the soy checkoff, using a North Dakota Ag Products Utilization Commission grant and in partnership with the North Dakota State University coating and polymeric materials department.
Dean Webster, a polymer chemist at NDSU, says soybean oil offers an appealing alternative for several reasons.
“Soybean oil can improve rubber’s sustainability without sacrificing performance relative to petrochemical products,” he says in a digital book called “Spurring Automotive Innovation with Soy,” published in partnership with the soy checkoff.
After research and development, the first RAPTOR belt made with soy oil was produced in 2014. It’s available for purchase in the U.S. and in 20 other countries.
“The whole concept (soy oil in rubber) is something that we are very excited about,” Vorhees says. “We think there is a lot of room to grow with a lot of possibilities.”
Myers is confident in the checkoff’s contributions to new ways to utilize the soybeans he grows.
“I like to see the new uses for soybeans,” he says. “What’s the next thing that will add profitability to the farm? There are all types of companies working on new products. What’s the next thing that will add $2 to every $1 of our checkoff investment?”
As a checkoff farmer-leader Myers says products like Goodyear tires produced with soy oil, the WCCO draper belts and soy-based asphalt make the soy checkoff that much more important.
“We’re working with a small percentage of everybody’s value of the soybeans and investing it in projects that will benefit all of us in the long run by adding more profit to the farm,” he says.